Cold Room Assembly – How to Build Cold Room With Own Hands
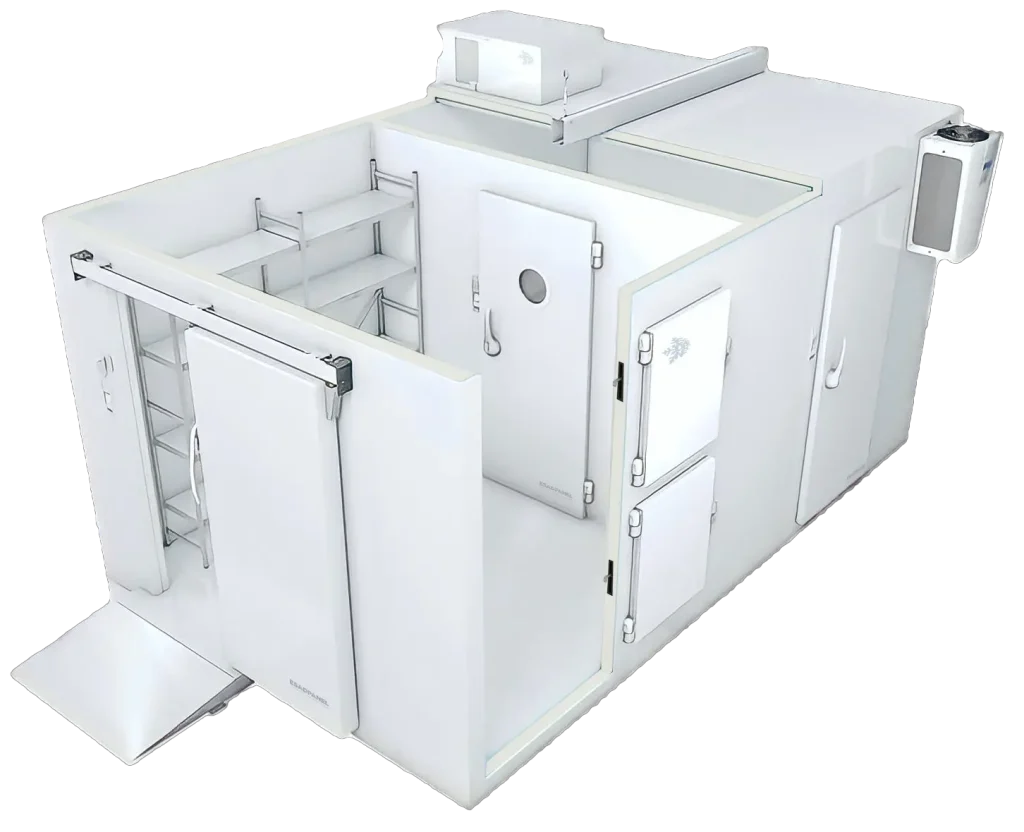
COLD STORAGE
CASE ASSEMBLY
Do you know how to assembly your cold room? Here is an article about installation!
How to build Cold Room and Freezer Storages With own hands?
In this article, you will know how to solve the problem with the selection and installation of a cold storage chamber for needs of your business. And also you can use these tips if you will need a large cooling chamber (from 4 cubic meters or 141 cubic foot) for a residential house.
The refrigerated chamber for storage of meat, vegetables and fruits, dairy and other products can be made without resorting to the help of specialists, but only in some simple cases.
There are three main ways:
- To buy a finished prefabricated cold room;
- To collect it from the heat-insulated sandwich panels;
- To upgrade the existing warehouse.
After completing the chamber, you must install the refrigeration equipment to maintain the desired temperature. Installing the equipment without the involvement of qualified personnel is difficult to perform; the only available option for such self-installation is a refrigeration monoblock (storage temperature is about 0 : +5 0С, +32 : +410F) or a freezer monoblock (-15 : -25 0С, +5 : -15 0F).
1. Prefabricate- Demountable Refrigeration Chambers
This is the easiest and fastest way to get a finished camera. The prefabricated chamber is a set of ready, heat-insulating sandwich panels with polyurethane filler with the special fastening of straight and corner junctures. In addition, such a chamber can be demounted and installed in a new location. The camera kit already includes a swing door. It remains to be determined the volume, the dimensions that you want to need and order it from one of the dealers of the manufacturer. Such a camera is not difficult to gather with the help of 2-3 people without special qualification. Prefabricated chambers are divided into two types, different in the connection type of the panels to each other:
- Profile plastic chambers with spike-groove joints (commonly called the ‘dovetail fastening’),
- Lock chambers (an eccentric lock, building into the sandwich panel).
These cameras with built-in eccentric locks provide a rigid fixed coupling of the panels among themselves, withstanding multiple assembly and disassembly. Chambers with spike-groove joints are cheaper, but require the using of sealants at the joints. And the plastic fastening is less rigid to the panels. Owing to this, such chambers rarely occur in width/length more than 2-3m. The price of a prefabricated camera will probably be somewhat larger than in two subsequent variants. However, it is an easy and fast way to access a good quality size, without the “bridges” of cold.
2. Fitting of Sandwich Panels
You can make a chamber by yourself out of the panels of the constructive type. In this case, you need to calculate a quantity of panels and their length which you want to buy. Their width varies from 1100 to 1200 mm in different manufacturers. Esad Panel provides in 1100mm/1,11cm. Based on this information and also the dimensions of the planned chamber, calculate the number and length of panels for your purchase. The assembly process itself, method of fastening the straight and angled joints you can specify in the documentation of the manufacturer you choose.
When mounting the panels, it is necessary to avoid the formation of “thermal bridges” at the corner joints when the inner and outer metal shells fall into their contact. To prevent the appearance of a thermal bridge, it is necessary to make its “rupture”, made a slit in the inner metal skin of the corner panel, in the part that “exits” to the outside of the chamber. Similarly, it is necessary to do within the corner joints of wall panels with the floor and ceiling panels. In the chambers with a storage temperature above zero, the floor is sometimes left without the thermal insulation. This simplifies the drive of used loading equipment (rollers, trolleys), saves money for the purchase of the thermal insulation materials, but at the same time requires the installation of refrigeration equipment with a higher capacity (about 20%) and, accordingly, leads with approximately the same increase in the electricity consumption. Also, it is necessary to perform an “operation” for breaking the “thermal bridge”, if you mount a multi-section chamber with different temperature regimes. It is necessary to cut through the inner metal covering of the walls, floor and ceiling at the installation site of the partition, tearing the thermal bridge between the sections. So, you will need to purchase the finishing accessories (batten, angle profile) for fixing corner joints of the panels, a sealant and a door of desired size. The door is also needed special, refrigeration with the thermal insulation made of polyurethane foam. Some producers of sandwich panels deal with the manufacturing of doors, and there are companies specializing in the production of doors only.
3. Reconstruction of the Premise
And the last option, often the cheapest, but not always eventually profitable, is the reconstruction of a warehouse or a room. These rooms can be made refrigerated by carrying out the thermal insulation of the walls. It can be made from the polyurethane foam sandwich panels, described in the previous point. In this version, these panels are fixed to the walls and ceiling of the premise with the help of fasteners. However, the metal fasteners will form many “thermal bridges”, which can lead to the formation of condensation and further rusting in the attachment points. Therefore, it is desirable to use fasteners made of the heat-insulating materials, for example, polyamide studs. But this option is more expensive and it is harder to work with it. The insulation can also be made of expanded polystyrene boards (PBP, foam plastic), urethane-foam mates (without metal sheathing), and also by foam polyurethane insulation spraying on the walls and ceilings. In these cases, it is necessary to insulate the thermal insulation layer with metal sheathing for mechanical protection and hygienic requirements. But this work is laborious and the result leaves much to be desired. It is much easier to use prefabricated panels. The option of thermal insulation of the walls, although it may be the cheapest, but does not guarantee the high-quality thermal insulation, and can also cause claims of the inspection bodies due to the non-compliance with hygienic requirements. When choosing a premise, it is necessary to take into account some features of storage for various food products and non-food items requiring cooling.
Fill the Form!
Write your needs and fill the form to contact us. Then get your cold room!