Things to Consider in Cold Room Installation
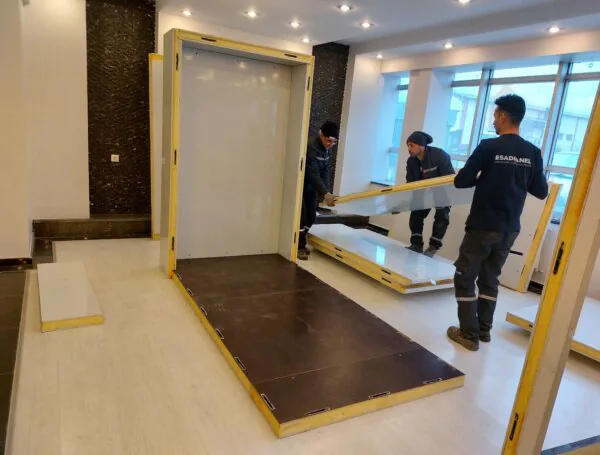
COLD STORAGE INSTALLATION
Cold rooms are essential for product preservation and energy efficiency. Poor installation can lead to high costs and performance issues. This article covers the key points for a successful cold room setup.
Things to Consider in Cold Storage Installation
Key Considerations in Cold Room Installation
Cold room systems are crucial in the food, pharmaceutical, chemical, and many other industries. For an efficient and long-lasting cold room, various factors must be considered during installation. Here are the key points to pay attention to when installing a cold room:
1. Proper Planning and Site Survey
Before starting the installation, the purpose of the cold room and the characteristics of the stored products must be considered. Accurate measurements should be taken, and a detailed site survey should be conducted for door and equipment placement. Additionally, the condition of the cold room floor and surrounding areas should be evaluated.
2. Floor and Surface Preparation
The installation site should have a smooth and solid floor. Floor slope, surface roughness, and insulation conditions must be checked. If necessary, insulation materials should be added to the floor, and appropriate coating should be applied.
3. Proper Panel Installation
Cold room insulation panels must be cut to the correct dimensions and joined seamlessly. The connection points of the panels should be carefully checked and securely locked using appropriate locking systems. Polyurethane foam or sealing materials should be applied to panel joints.
4. Proper Door and Seal Placement
Cold room doors must provide excellent insulation to prevent heat loss. Door seals should be properly fitted and free of damage. Additionally, hinge and lock mechanisms should be inspected for smooth operation.
5. Proper Placement of Cooling Units
Cooling units should be positioned to ensure optimal airflow within the room. Adequate spacing must be maintained for proper air circulation, and clearances from walls and ceilings should be considered. Accessibility for maintenance and repair should also be taken into account.
6. Insulation and Air Tightness
To ensure the efficiency of the cold room, heat loss must be minimized. All connection points and corners should be reinforced with insulation materials. If air leakage is not prevented, the cold room will suffer from energy loss and reduced efficiency.
7. Electrical and Control Systems
The electrical installation of cold rooms must ensure the safe operation of cooling units and other systems. Wiring should be resistant to humidity and low-temperature conditions. Automation systems should be integrated to monitor temperature, humidity, and alarm mechanisms continuously.
8. Testing and Commissioning Process
After installation is complete, all components must be tested for proper operation. The cooling system should be activated, and temperature controls must be performed to ensure the desired temperature is achieved. Additionally, door sealing, air leaks, and electrical systems should be thoroughly inspected.
9. Common Mistakes and Solutions
Incorrect measurement and planning: Wrong measurements lead to installation errors. Proper site survey and planning are essential.
Improper panel fitting: Gaps between panel joints cause insulation loss. Panels must be tightly assembled.
Door sealing issues: Door seals should be regularly inspected and replaced when necessary.
Incorrect placement of cooling units: Units should be positioned to allow unrestricted airflow.
Considering these factors in cold room installation ensures long-lasting, energy-efficient, and trouble-free operation. Proper material selection, professional installation, and regular maintenance will enhance the performance of cold rooms.
Fill the Form!
Write your needs and fill the form to contact us. Then get your cold room!